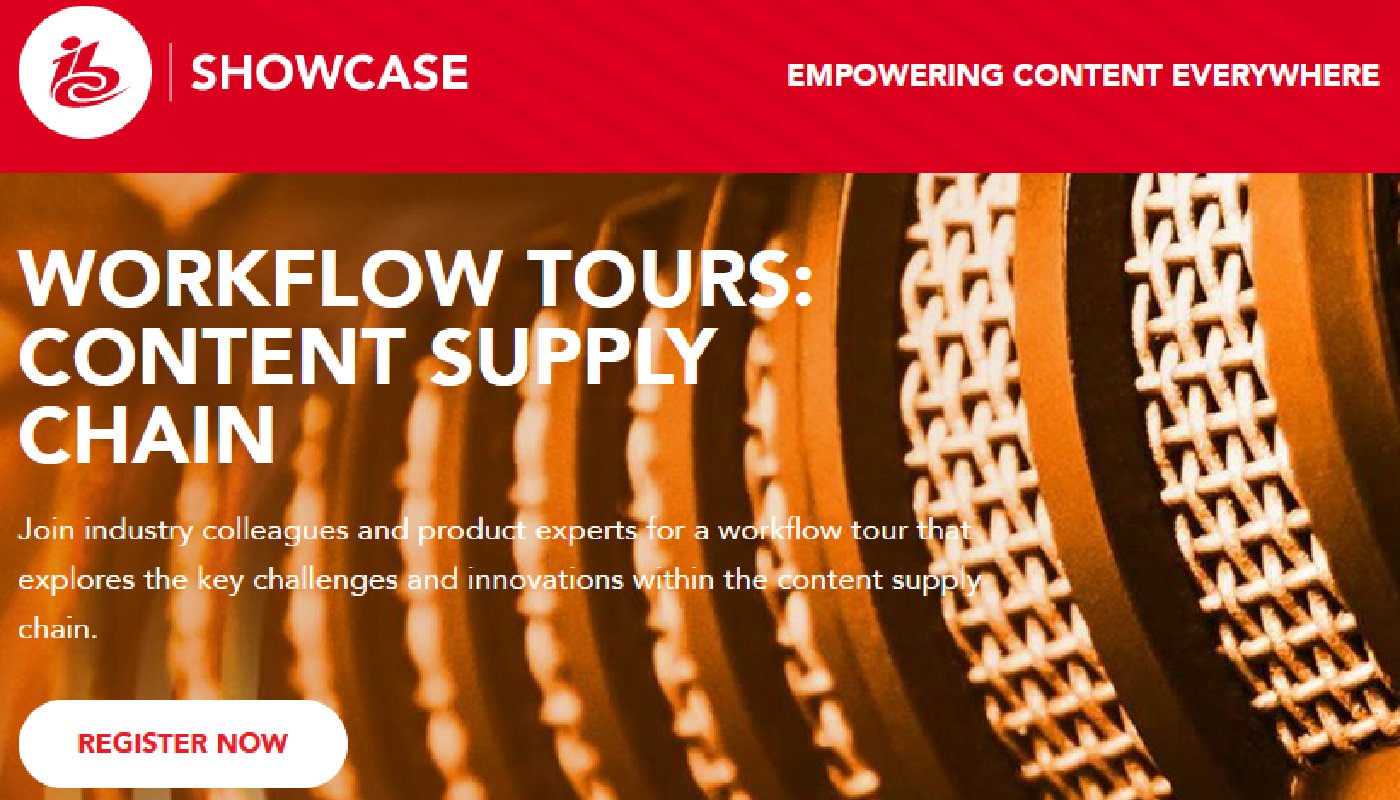
There is always risk, regardless of industry. There is always risk, regardless of whether it is the industry or the business itself. It is possible to reduce the risk by identifying the risks and then implementing appropriate controls.
An important concept for any organization is inherent risk. It is an estimated degree of risk in a particular process or operation before any controls are applied. The complexity of a process may increase the risk. But it doesn't have to be. It is possible for the risk to be very low in certain cases but still pose a significant risk.
Inherent risk is also a good indicator of the degree of risk that an organization faces. For example, if an organization has a weak IT infrastructure, it will likely have higher inherent risk. Because the infrastructure of an organization is vulnerable to attack, this is why it will have a higher inherent risk. This is why it is crucial for organizations to have plans in place for monitoring their security status. They should include cybersecurity controls.
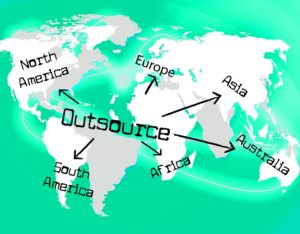
One example of an inherent danger would be a company with no antivirus software installed on their computer systems. If an attacker is able to install malware on the computer, there is a risk that the data will be stolen. The chances of internal information theft are reduced if there is a robust logging and monitoring system.
FFIEC created an assessment protocol to aid financial institutions in evaluating their risk. The protocol is a framework that allows you to determine the value at risks (VaR) for a specific process. This protocol can be used to help identify risks before they could cause harm. However, it should be noted that this is a simple assessment and the process may not be as accurate as it could be.
It is also crucial to know the difference between inherent risk and residual risk. These are two completely different concepts. It is possible for an organization to have a strong IT system, but still face residual risks. This is because the organization must constantly evaluate its risk tolerance. It is best to use a systematic approach to risk assessment.
Residual is a risk that continues to exist, despite the best efforts made by security personnel and organizations. A residual risk assessment will help identify exposures that may be exploited by cybercriminals before they even occur. A residual risk assessment will also consider the influence of security controls on a given exposure. FFIEC advises that organizations have a solid set of controls to reduce the risk of residual danger.
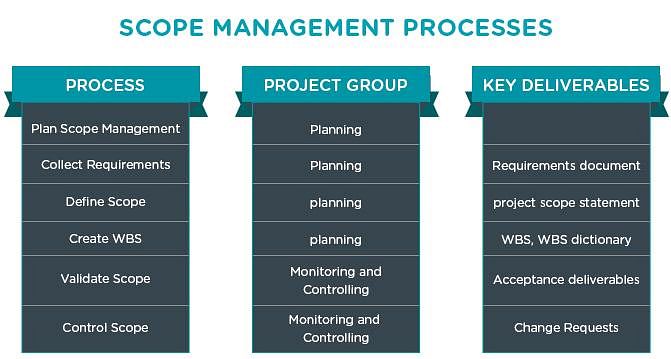
However, residual risk does not have to be evaluated without considering the value of inherent risk. While residual risk can be measured before the controls are implemented, it can also been measured after they have been applied. This can help to assess how effective the controls have been.
FAQ
What kind people use Six Sigma?
Six Sigma will most likely be familiar to people who have worked in statistics and operations research. It can be used by anyone in any business aspect.
This requires a lot of dedication, so only people with great leadership skills can make the effort to implement it.
What are the 4 main functions of management?
Management is responsible in planning, organizing and directing people and resources. Management also involves setting goals and developing policies.
Organizations can achieve their goals through management. This includes leadership, coordination, control and motivation.
The following are the four core functions of management
Planning - Planning refers to deciding what is needed.
Organizing - Organizing involves deciding how things should be done.
Directing – This means to get people to follow directions.
Controlling - This is the ability to control people and ensure that they do their jobs according to plan.
What is TQM, exactly?
The industrial revolution led to the birth and growth of the quality movement. Manufacturing companies realized they couldn't compete solely on price. They had to improve efficiency and quality if they were to remain competitive.
In response to this need for improvement, management developed Total Quality Management (TQM), which focused on improving all aspects of an organization's performance. It included continual improvement processes, employee involvement, customer satisfaction, and customer satisfaction.
What are the 5 management processes?
The five stages of a business include planning, execution (monitoring), review, evaluation, and review.
Setting goals for the future is part of planning. Planning involves defining your goals and how to get there.
Execution occurs when you actually carry out the plans. Everyone involved must follow them.
Monitoring is the process of evaluating your progress toward achieving your objectives. This should involve regular reviews of performance against targets and budgets.
Every year, there are reviews. They provide an opportunity to assess whether everything went well during the year. If not then, you can make changes to improve your performance next year.
After the annual review, evaluation takes place. It helps identify what worked well and what didn't. It also provides feedback on the performance of people.
What is Six Sigma, exactly?
It's an approach to quality improvement that emphasizes customer service and continuous learning. The goal is to eliminate defects by using statistical techniques.
Motorola created Six Sigma as part of their efforts to improve manufacturing processes in 1986.
The idea spread quickly throughout the industry, and today, many organizations are using six sigma methods to improve product design, production, delivery, and customer service.
What are your main management skills
Business owners need to have management skills, no matter how small or large they may be. They are the ability to manage people and finances, space, money, and other factors.
Management Skills are also needed when you're setting goals and objectives, planning strategies, leading teams, motivating employees, resolving problems, creating policies and procedures, and managing change.
As you can see, there's no end to the list of managerial duties!
Statistics
- The average salary for financial advisors in 2021 is around $60,000 per year, with the top 10% of the profession making more than $111,000 per year. (wgu.edu)
- This field is expected to grow about 7% by 2028, a bit faster than the national average for job growth. (wgu.edu)
- 100% of the courses are offered online, and no campus visits are required — a big time-saver for you. (online.uc.edu)
- Your choice in Step 5 may very likely be the same or similar to the alternative you placed at the top of your list at the end of Step 4. (umassd.edu)
- Our program is 100% engineered for your success. (online.uc.edu)
External Links
How To
How can you implement the Kaizen technique?
Kaizen means continuous improvement. The Japanese philosophy emphasizes small, incremental improvements to achieve continuous improvement. This term was created by Toyota Motor Corporation in 1950. It's a team effort to continuously improve processes.
Kaizen is one method that Lean Manufacturing uses to its greatest advantage. The concept involves employees responsible for manufacturing identifying problems and trying to fix them before they become serious issues. This is how you can improve the quality and lower the cost.
Kaizen is a way to raise awareness about what's happening around you. So that there is no problem, you should immediately correct it if something goes wrong. It is important that employees report any problems they see while on the job to their managers.
There are some basic principles that we follow when doing kaizen. We always start from the end product and move toward the beginning. If we want to improve our factory for example, we start by fixing the machines that make the final product. Next, we repair the machines that make components. Then, the machines that make raw materials. We then fix the workers that work with those machines.
This method is known as kaizen because it focuses upon improving every aspect of the process step by step. We finish fixing the factory and then go back to the beginning. This continues until we achieve perfection.
You need to know how to measure the effectiveness of kaizen within your business. There are several ways that you can tell if your kaizen system is working. One of these ways is to check the number of defects found on the finished products. Another way is determining how much productivity increased after implementing kaizen.
You can also find out if kaizen works by asking yourself why you decided to implement it. It was because of the law, or simply because you wanted to save some money. Did you really think that it would help you achieve success?
If you answered yes to any one of these questions, congratulations! You are now ready to begin kaizen.