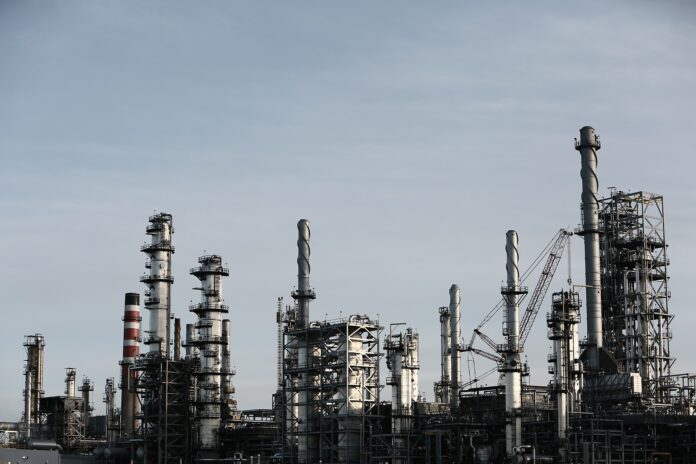
What is supply chain management? Supply chain management refers a process for managing commerce. It includes all aspects of the supply chain from raw materials to work-in process inventory to the final order fulfillment. We will now discuss the different aspects of supply chain management. Let's take a look at four components of a supply network to help you better understand them. Listed below are the benefits of supply chain management and how it can benefit your business.
Product portfolio planning
Portfolio planning is a tool that helps companies develop new products and manage inventories to meet changing market needs. The concept also involves monitoring project resource consumption. Proper financial management can boost cash flow and supplement current expenses. Planning for new products often involves several departments within a company. This can lead to miscommunications and disconnect. This can be avoided by making sure communication channels are open and checking on progress regularly.
The long-term vision of the company and its business strategy are essential to successfully implement a product collection. If a company aligns its current projects to the long-term business goals, it can expect increased sales and profits as well as greater market share. Companies can use product portfolio planning to determine which products will be most profitable and provide the best return on their investment. It also allows companies to determine which products are redundant and which are cash cows.
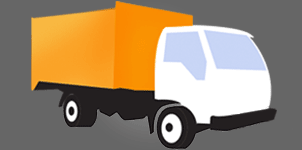
Distribution planning
Distribution planning, also called distribution requirements planning (DRP), is a systematic process that determines how much of each good to produce and where to store them. This type of planning helps to reduce shortages and minimize costs when ordering. It also considers how many products are needed in a particular region. It employs a tree structure to calculate the gross supply requirements for a supplier and the inventory each item will require. Manufacturers can use a DRP tool to optimize their key performance indicator(s) in order to determine which distribution plan will yield the highest profit margin.
Distribution planning is an integral part of supply chain management. It involves many sub-discipline techniques that make it more efficient. Just-in-time inventory is one of these practices. Distribution is key to success because there are so many moving parts. It is crucial to have a strong distribution management strategy. This also requires real-time data. Here are some key components to a successful distribution strategy.
Sales and operations planning
S&OP (sales & operations planning) is a process that's used in supply chain control to coordinate activities among business units and achieve profitability. S&OP can either be performed on a monthly or annual basis. It involves demand and supply planning, forecasting, and executive reviews. The ultimate goal is to make customers happy and to increase profits. This process is not limited to spreadsheets and should be used by companies with more than one location.
No matter how large the company is, strong leadership and central figures are essential for effective sales and operations planning. It is important to encourage cohesion among conflicting parts of the business. However, a central figure must be present to ensure that these standards are met. The leader of the sales department should be an active participant in the process, and his or her role should be to ensure that the process is carried out correctly.
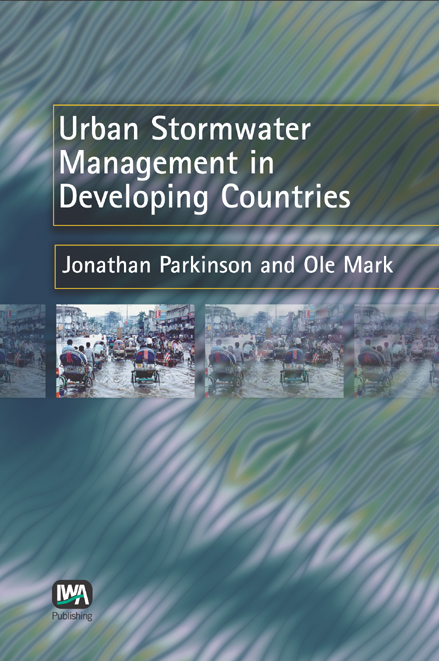
Planned Trade Promotion
Trade Promotion Planning can be a crucial part of any company's success. Trade promotion refers to the marketing activity that a manufacturer does with a retailer. This may include discounts, promotions, coupons, and other tools to increase retailer demand, ultimately increasing sales. These are the essential elements of trade promotion planning. A trade promotion strategy that is successful will include the following elements:
Promotion planning refers to the management of special events, other than a forecast. This planning process includes calculating the impact of a promotion using causal strategies and projecting these into specific periods in the future. It is used to plan marketing strategies for one-off or repeated events. Consensus demand planning is the combination of multiple data sources to produce a consensus plan. This involves many activities such as safety stock planning and distribution planning.
FAQ
What is Kaizen?
Kaizen refers to a Japanese term that stands for "continuous improvements." It is a philosophy which encourages employees in continuously improving their work environment.
Kaizen is founded on the belief of everyone being able to do their job well.
How does a manager motivate his/her employees?
Motivation refers to the desire or need to succeed.
It is possible to be motivated by doing something you enjoy.
You can also get motivated by seeing your contribution to the success or the improvement of the organization.
If you are a doctor and want to be one, it will likely be more rewarding to see patients than to read medical books every day.
The inner motivation is another type.
You might feel a strong sense for responsibility and want to help others.
Or you might enjoy working hard.
If you don’t feel motivated, find out why.
Next, think of ways you can improve your motivation.
Which kind of people use Six Sigma
Six Sigma is well-known to those who have worked in operations research and statistics. Anyone involved in business can benefit.
This requires a lot of dedication, so only people with great leadership skills can make the effort to implement it.
What is the difference in leadership and management?
Leadership is about influencing others. Management is about controlling others.
A leader inspires his followers while a manager directs the workers.
Leaders motivate people to succeed; managers keep workers on track.
A leader develops people; a manager manages people.
What are some common management mistakes?
Managers sometimes make their own job harder than necessary.
They might not give enough support and delegate the right responsibilities to their staff.
A majority of managers lack the communication skills needed to motivate their team and lead them.
Some managers set unrealistic expectations for their staff.
Some managers may try to solve every problem themselves instead of delegating responsibility to others.
Statistics
- The profession is expected to grow 7% by 2028, a bit faster than the national average. (wgu.edu)
- The average salary for financial advisors in 2021 is around $60,000 per year, with the top 10% of the profession making more than $111,000 per year. (wgu.edu)
- Your choice in Step 5 may very likely be the same or similar to the alternative you placed at the top of your list at the end of Step 4. (umassd.edu)
- Hire the top business lawyers and save up to 60% on legal fees (upcounsel.com)
- The BLS says that financial services jobs like banking are expected to grow 4% by 2030, about as fast as the national average. (wgu.edu)
External Links
How To
What is Lean Manufacturing?
Lean Manufacturing processes are used to reduce waste and improve efficiency through structured methods. They were created in Japan by Toyota Motor Corporation during the 1980s. The aim was to produce better quality products at lower costs. Lean manufacturing seeks to eliminate unnecessary steps and activities in the production process. It is made up of five elements: continuous improvement, continuous improvement, just in-time, continuous change, and 5S. The production of only what the customer needs without extra work is called pull systems. Continuous improvement means continuously improving on existing processes. Just-in time refers to components and materials being delivered right at the place they are needed. Kaizen is continuous improvement. This can be achieved by making small, incremental changes every day. Last but not least, 5S is for sort. To achieve the best results, these five elements must be used together.
Lean Production System
Six key concepts are the basis of lean production:
-
Flow is about moving material and information as near as customers can.
-
Value stream mapping - Break down each stage in a process into distinct tasks and create an overview of the whole process.
-
Five S's: Sort, Shine Standardize, Sustain, Set In Order, Shine and Shine
-
Kanban: Use visual signals such stickers, colored tape, or any other visual cues, to keep track your inventory.
-
Theory of constraints: identify bottlenecks in your process and eliminate them using lean tools, such as kanban board.
-
Just-in-time delivery - Deliver components and materials right to your point of use.
-
Continuous improvement - Make incremental improvements rather than overhauling the entire process.